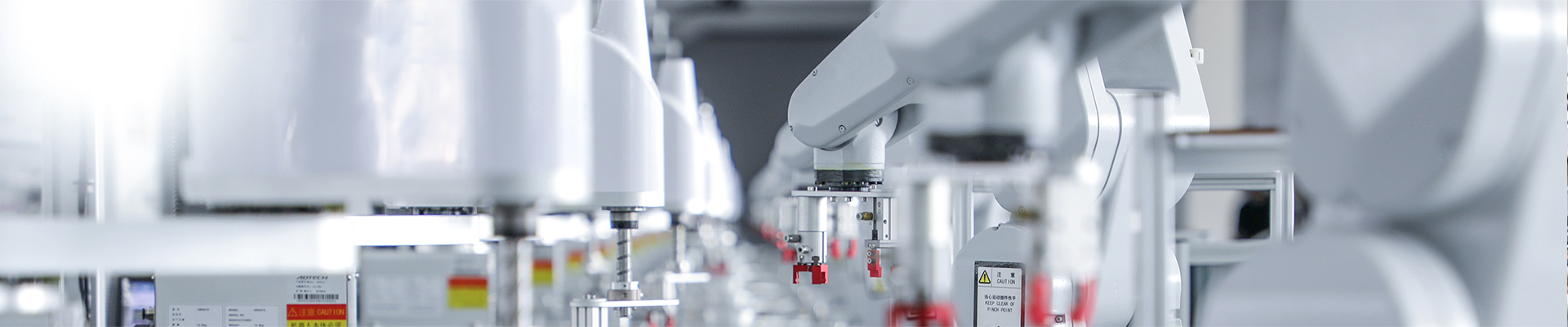
What are the best practices for maintaining Power Lines Stringing Machines to ensure longevity and optimal performance in the field?
2025-07-20Regular and meticulous maintenance is critical for the long operational life and reliable performance of power lines stringing machines:
-
Adhere to Manufacturer's Schedule: Strictly follow the maintenance schedule outlined in the machine's operation and maintenance manual, including daily checks, weekly inspections, and periodic major servicing.
-
Hydraulic System Care: Regularly check hydraulic fluid levels and quality, replace hydraulic filters promptly, and inspect all hoses, fittings, and cylinders for leaks or damage. Use only recommended hydraulic fluid types.
-
Engine Maintenance: Perform routine engine oil and filter changes, air filter inspections/replacements, and fuel filter maintenance. Monitor engine performance and address any unusual noises or warning lights immediately.
-
Bullwheel/Capstan Inspection: Daily inspection for wear, damage, or degradation of the lining material. Any grooves, nicks, or foreign material can damage conductors. Replace linings as needed.
-
Braking System Checks: Regularly inspect and test all braking components, including disc brakes, calipers, and emergency brake mechanisms, to ensure optimal stopping power and safety.
-
Lubrication: Consistently lubricate all grease points and moving parts (e.g., bearings, pivot points) with the recommended lubricants.
-
Structural Integrity: Periodically inspect the machine frame, chassis, and attachment points for cracks, corrosion, or deformation. Ensure all bolts and fasteners are tightened to specification.
-
Calibration: Periodically calibrate load cells, dynamometers, and control systems to ensure accurate readings for tension, speed, and length.
-
Cleanliness & Storage: Keep the machine clean, especially control panels and hydraulic components. Store the machine under cover when not in use to protect it from harsh weather.